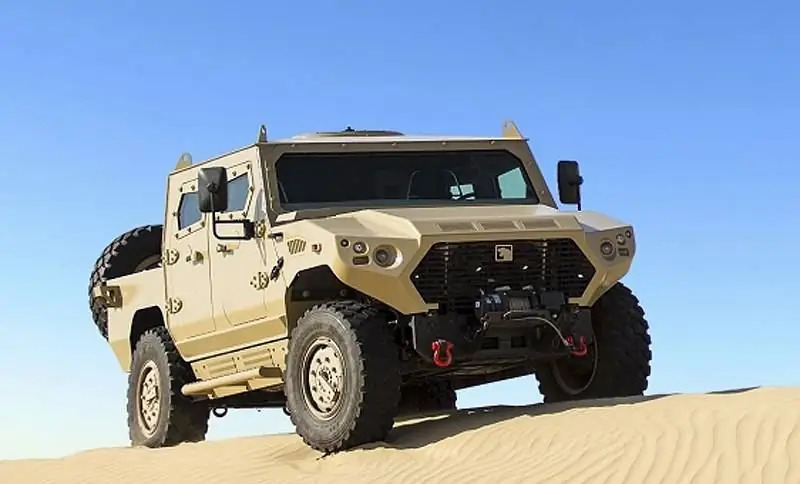
Armor berjuta-juta tahun lebih tua dari manusia, dan ia dikembangkan terutamanya untuk melindungi dari rahang dan cakar. Ada kemungkinan bahawa buaya dan kura-kura dapat menginspirasi manusia untuk membuat elemen pelindung. Semua senjata tenaga kinetik, sama ada kelab prasejarah atau peluru menembus baju besi, dirancang untuk memusatkan kekuatan besar di kawasan kecil, tugasnya adalah menembus sasaran dan menimbulkan kerosakan maksimum di atasnya. Akibatnya, tugas perisai adalah mencegahnya dengan memesongkan atau memusnahkan alat penyerang dan / atau menyebarkan tenaga hentaman ke kawasan seluas mungkin untuk mengurangkan kerosakan tenaga kerja, sistem pengangkutan dan struktur yang dilindunginya.
Perisai moden biasanya terdiri daripada lapisan luar yang keras untuk menghentikan, memesongkan, atau memusnahkan proyektil, lapisan perantaraan dengan "kerja pecah" yang sangat tinggi, dan lapisan dalam yang likat untuk mencegah retakan dan serpihan.
Keluli
Baja, yang menjadi bahan pertama yang digunakan secara meluas dalam pembuatan kenderaan berperisai, masih diminati, walaupun terdapat perisai berdasarkan aloi ringan dari aluminium dan titanium, seramik, komposit dengan matriks polimer, diperkuat dengan gentian kaca, aramid dan polietilena berat molekul ultra tinggi, serta bahan komposit dengan matriks logam.
Banyak kilang keluli, termasuk SSAB, terus mengembangkan keluli berkekuatan tinggi untuk pelbagai aplikasi kritikal seperti pelapisan tambahan. Keluli berperisai ARM OX 600T, tersedia pada ketebalan 4-20 mm, tersedia dengan kekerasan terjamin 570 hingga 640 unit HBW (singkatan untuk Kekerasan, Brinell, Wolfram; ujian di mana bola tungsten dengan diameter standard ditekan menjadi sampel bahan dengan daya yang diketahui, maka diameter ceruk yang terbentuk diukur; maka parameter ini diganti dengan formula, yang memungkinkan anda memperoleh jumlah unit kekerasan).
SSAB juga menekankan pentingnya mencapai keseimbangan kekerasan dan ketangguhan yang tepat untuk penembusan dan perlindungan pecah. Seperti semua keluli, ARMOX 600T terdiri daripada besi, karbon dan sejumlah komponen paduan lain termasuk silikon, mangan, fosfor, sulfur, kromium, nikel, molibdenum, dan boron.
Terdapat batasan pada teknik pembuatan yang digunakan, terutama dalam hal suhu. Baja ini tidak dimaksudkan untuk rawatan haba tambahan; jika dipanaskan di atas 170 ° C selepas penghantaran, SSAB tidak dapat menjamin sifatnya. Syarikat yang dapat mengatasi sekatan semacam ini cenderung menarik perhatian ketat pengeluar kenderaan berperisai.
Syarikat Sweden yang lain, Deform, menawarkan bahagian besi pelindung tahan panas peluru kepada pengeluar kenderaan berperisai, terutama yang ingin meningkatkan perlindungan kenderaan komersial / awam.
Firewall satu bahagian dipasang di Nissan PATROL 4x4, minibus Volkswagen T6 TRANSPORTER, dan trak pikap Isuzu D-MAX, bersama dengan kepingan lantai padat dari bahan yang sama. Proses pembentukan panas yang dikembangkan oleh Deform dan digunakan dalam pengeluaran lembaran mengekalkan kekerasan 600HB [HBW].
Syarikat itu mendakwa bahawa ia dapat mengembalikan sifat semua baja perisai di pasaran sambil mengekalkan bentuk yang ditentukan secara struktur, sementara bahagian yang dihasilkan jauh lebih unggul daripada struktur dikimpal tradisional dan sebahagiannya bertindih. Dalam kaedah yang dikembangkan oleh Deform, kepingan dilenyapkan dan dikeringkan setelah penempaan panas. Berkat proses ini, adalah mungkin untuk memperoleh bentuk tiga dimensi yang tidak dapat diperoleh dengan pembentukan sejuk tanpa wajib dalam kes seperti itu "pengelasan yang melanggar integriti titik kritikal."
Lembaran keluli bentuk panas yang cacat telah digunakan pada BAE Systems BVS-10 dan CV90 dan, sejak awal tahun 1990-an, pada banyak mesin Kraus-Maffei Wegmann (KMW). Perintah datang untuk pengeluaran plat perisai tiga dimensi untuk tangki LEOPARD 2 dan beberapa plat berbentuk untuk kenderaan BOXER dan PUMA, ditambah untuk beberapa kenderaan Rheinmetall, termasuk sekali lagi BOXER, serta menetas untuk kenderaan WIESEL. Deform juga berfungsi dengan bahan pelindung lain termasuk aluminium, kevlar / aramid dan titanium.
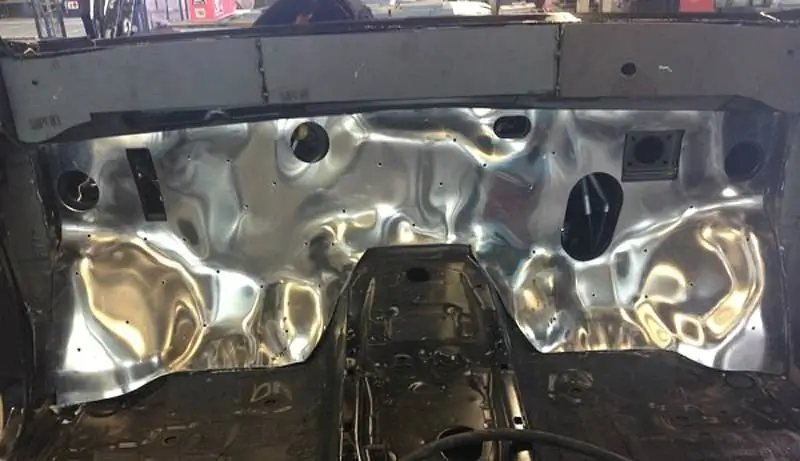
Kemajuan aluminium
Bagi kenderaan berperisai, buat pertama kalinya perisai aluminium digunakan secara meluas dalam pembuatan kapal induk perisai M113, yang telah dihasilkan sejak tahun 1960. Ia adalah aloi, yang ditetapkan 5083, mengandungi 4.5% magnesium dan jumlah mangan, besi, tembaga, karbon, zink, kromium, titanium dan lain-lain yang jauh lebih kecil. Walaupun 5083 mengekalkan kekuatannya dengan baik selepas kimpalan, ia bukan aloi yang boleh dirawat dengan haba. Ia tidak mempunyai ketahanan yang baik terhadap peluru menembus perisai 7.62mm, tetapi, seperti yang disahkan oleh ujian rasmi, ia menghentikan peluru menembus baju besi gaya Soviet 14.5mm lebih baik daripada keluli, sambil menjimatkan berat badan dan menambahkan kekuatan yang diinginkan. Untuk tahap perlindungan ini, kepingan aluminium lebih tebal dan 9 kali lebih kuat daripada keluli dengan ketumpatan yang lebih rendah 265 r / cm3, yang mengakibatkan pengurangan berat struktur.
Pengilang kenderaan berperisai segera mula meminta perisai aluminium yang lebih ringan, lebih kuat secara balistik, boleh dikimpal dan diperlakukan dengan panas, yang menyebabkan perkembangan Alcan pada tahun 7039 dan kemudian 7017, keduanya dengan kandungan zink yang lebih tinggi.
Seperti keluli, stamping dan pemasangan seterusnya boleh memberi kesan negatif terhadap sifat pelindung aluminium. Semasa mengimpal, zon yang terkena panas melembutkan, tetapi kekuatannya dipulihkan sebahagiannya kerana pengerasan semasa penuaan semula jadi. Struktur logam berubah pada zon sempit berhampiran kimpalan, mewujudkan tegangan sisa yang besar sekiranya berlaku kesalahan pengelasan dan / atau pemasangan. Oleh itu, teknik pembuatan harus meminimumkannya, sementara risiko keretakan kakisan tekanan juga harus diminimumkan, terutama ketika jangka hayat mesin diharapkan lebih dari tiga dekad.
Keretakan kakisan tekanan adalah proses penampilan dan pertumbuhan retakan di persekitaran yang menghakis, yang cenderung merosot apabila bilangan unsur paduan meningkat. Pembentukan retakan dan pertumbuhannya seterusnya berlaku akibat penyebaran hidrogen di sepanjang batas butiran.
Penentuan kerentanan terhadap retak bermula dengan pengekstrakan sejumlah kecil elektrolit dari retakan dan analisisnya. Ujian kakisan tegangan kadar regangan rendah dilakukan untuk menentukan seberapa teruk aloi tertentu telah rosak. Peregangan mekanikal dua sampel (satu di persekitaran yang menghakis, dan yang lain di udara kering) berlaku sehingga mereka gagal, dan kemudian ubah bentuk plastik di tapak patah dibandingkan - semakin banyak sampel diregangkan ke kegagalan, semakin baik.
Ketahanan terhadap keretakan kakisan tekanan dapat ditingkatkan semasa pemprosesan. Sebagai contoh, menurut Total Materia, yang menyebut dirinya "pangkalan data bahan terbesar di dunia," Alcan telah meningkatkan prestasi 7017 dalam ujian retak kakisan tekanan dipercepat sebanyak 40 kali. Hasil yang diperoleh juga memungkinkan untuk mengembangkan kaedah perlindungan kakisan untuk zon struktur yang dikimpal, di mana sukar untuk mengelakkan tekanan sisa. Penyelidikan bertujuan meningkatkan aloi untuk mengoptimumkan ciri elektrokimia sendi yang dikimpal sedang dijalankan. Mengusahakan aloi yang boleh dirawat haba baru memberi tumpuan kepada peningkatan kekuatan dan ketahanan kakisannya, sementara kerja pada aloi yang tidak dapat dirawat haba bertujuan untuk menghilangkan kekangan yang dikenakan oleh keperluan kebolehkimpalan. Bahan paling sukar dalam pembangunan akan menjadi 50% lebih kuat daripada perisai aluminium terbaik yang digunakan sekarang.
Aloi berketumpatan rendah seperti aluminium litium menawarkan penjimatan berat sekitar 10% berbanding aloi sebelumnya dengan ketahanan peluru yang setanding, walaupun prestasi balistik belum dapat dinilai sepenuhnya menurut Total Materia.
Kaedah pengelasan, termasuk kaedah robotik, juga bertambah baik. Antara tugas yang diselesaikan adalah meminimumkan bekalan haba, lengkungan kimpalan yang lebih stabil kerana peningkatan sistem bekalan tenaga dan wayar, serta pemantauan dan pengendalian proses oleh sistem pakar.
Bahan Lanjutan MTL bekerjasama dengan ALCOA Defense, pengeluar plat perisai aluminium yang terkenal, untuk mengembangkan apa yang digambarkan oleh syarikat sebagai "proses pembentukan sejuk yang boleh dipercayai dan berulang." Syarikat itu menyatakan bahawa aloi aluminium yang dikembangkan untuk aplikasi perisai tidak dirancang untuk pembentukan sejuk, yang bermaksud proses barunya harus membantu mengelakkan mod kegagalan biasa, termasuk keretakan. Tujuan utamanya adalah untuk membolehkan pereka mesin meminimumkan keperluan pengelasan dan mengurangkan bilangan bahagian, menurut syarikat itu. Mengurangkan jumlah kimpalan, syarikat menekankan, meningkatkan kekuatan struktur dan perlindungan kru sambil mengurangkan kos pengeluaran. Bermula dengan aloi 5083-H131 yang terbukti dengan baik, syarikat mengembangkan proses untuk membentuk bahagian sejuk dengan sudut selekoh 90 darjah di sepanjang dan melintasi butiran, kemudian beralih ke bahan yang lebih kompleks, misalnya, aloi 7017, 7020 dan 7085, juga mencapai hasil yang baik.
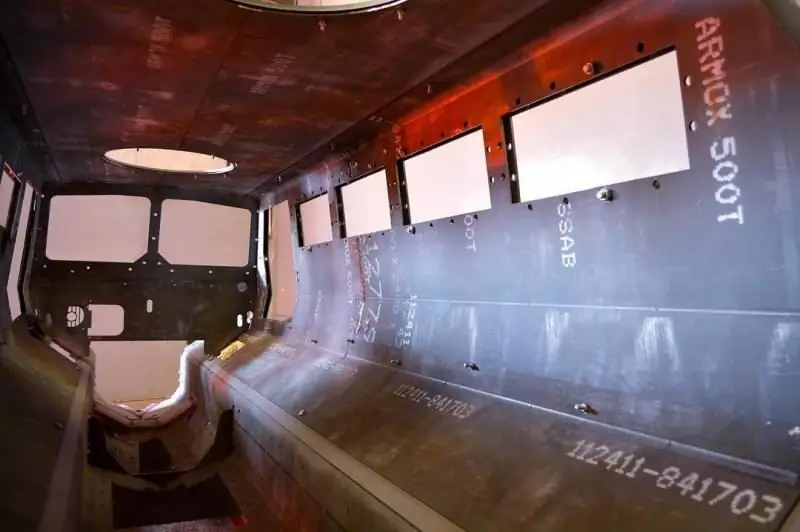
Seramik dan komposit
Beberapa tahun yang lalu, Morgan Advanced Materials mengumumkan pengembangan beberapa sistem perisai SAMAS, yang terdiri daripada gabungan seramik canggih dan komposit struktur. Lini produk merangkumi perisai berengsel, lapisan anti-fragmentasi, kapsul daya tahan yang diperbuat daripada komposit struktur untuk menggantikan lambung logam dan melindungi modul senjata, baik yang dihuni dan juga tidak berpenghuni. Kesemuanya dapat disesuaikan dengan keperluan tertentu atau dibuat mengikut pesanan.
Memberi perlindungan STANAG 4569 Tahap 2-6, bersama dengan prestasi pelbagai hambatan dan penjimatan berat (syarikat mendakwa sistem ini beratnya separuh daripada produk keluli yang serupa), dan menyesuaikan diri dengan ancaman, platform dan misi tertentu … Lapisan anti pecah boleh dibuat dari panel rata dengan berat 12.3 kg untuk meliputi kawasan seluas 0.36 m2 (sekitar 34 kg / m2) atau kelengkapan padat dengan berat 12.8 kg untuk 0.55 m2 (sekitar 23.2 kg / m2).
Menurut Morgan Advanced Materials, perisai tambahan yang direka untuk pemodenan baru dan pemodenan platform yang ada menawarkan kemampuan yang sama pada separuh berat. Sistem yang dipatenkan memberikan perlindungan maksimum terhadap berbagai macam ancaman, termasuk senjata berkaliber kecil dan sederhana, alat peledak improvisasi (IED) dan granat yang didorong oleh roket, serta prestasi multi-impak.
Sistem perisai "semi-struktur" dengan ketahanan kakisan yang baik ditawarkan untuk modul senjata (selain aplikasi udara dan laut), dan bersama dengan menjimatkan berat badan dan mengurangkan masalah dengan pusat graviti, tidak seperti keluli, ia mewujudkan masalah keserasian elektromagnetik yang lebih sedikit.
Perlindungan modul senjata adalah masalah tertentu, karena merupakan sasaran yang menarik, kerana pelumpuhannya secara drastik akan mengganggu arahan kru situasi dan kemampuan kenderaan untuk menangani ancaman di dekatnya. Mereka juga mempunyai optoelektronik halus dan motor elektrik yang rentan. Oleh kerana mereka biasanya dipasang di bahagian atas kenderaan, perisai harus ringan agar pusat graviti serendah mungkin.
Sistem perlindungan modul senjata, yang boleh merangkumi kaca perisai dan perlindungan bahagian atas, dapat dilipat sepenuhnya, dua orang dapat memasangnya kembali dalam 90 saat. Kapsul daya tahan komposit dibuat dari apa yang digambarkan oleh syarikat sebagai "bahan sukar dan formulasi polimer yang unik," mereka memberikan perlindungan pecahan peluru dan dapat diperbaiki di lapangan.
Perlindungan askar
SPS (Soldier Protection System) yang dikembangkan oleh 3M Ceradyne merangkumi topi keledar dan sisipan di perisai badan untuk Sistem Perlindungan Kepala Bersepadu (IHPS) dan VTP (Vital Torso Protection) - komponen ESAPI (Enhanced Small Arms Protective Insert) - sisipan yang lebih baik untuk perlindungan daripada senjata kecil) sistem SPS.
Keperluan IHPS merangkumi berat yang lebih ringan, perlindungan pendengaran pasif dan perlindungan hentaman tumpul yang lebih baik. Sistem ini juga merangkumi aksesori seperti komponen untuk melindungi rahang bawah seorang askar, pelindung, pelindung untuk kacamata penglihatan malam, panduan, misalnya, lampu suluh dan kamera, dan pelindung peluru modular tambahan. Kontrak itu, bernilai lebih dari $ 7 juta, menyediakan bekalan sekitar 5,300 helmet. Sementara itu, lebih daripada 30,000 kit ESAPI - sisipan yang lebih ringan untuk perisai badan - akan dihantar di bawah kontrak bernilai $ 36 juta. Pengeluaran kedua-dua kit ini bermula pada tahun 2017.
Juga di bawah program SPS, KDH Defense memilih bahan SPECTRA SHIELD dan EMAS EMAS Honeywell untuk lima subsistem, termasuk subsistem Perlindungan Torso dan Ekstremiti (TEP) yang akan dibekalkan untuk projek SPS. Sistem perlindungan TEP lebih ringan 26%, yang akhirnya mengurangkan berat sistem SPS sebanyak 10%. KDH akan menggunakan SPECTRA SHIELD, yang berdasarkan serat UHMWPE, dan GOLD SHIELD, berdasarkan serat aramid, dalam produknya sendiri untuk sistem ini.
Serat SPECTRA
Honeywell menggunakan proses pemintalan dan penggambaran serat polimer proprietari untuk memasukkan bahan mentah UHMWPE ke dalam serat SPECTRA. Bahan ini 10 kali lebih kuat daripada keluli dari segi berat, kekuatan spesifiknya 40% lebih tinggi daripada serat aramid, ia mempunyai titik lebur yang lebih tinggi daripada polietilena standard (150 ° C) dan ketahanan haus yang lebih tinggi berbanding polimer lain, kerana contohnya, poliester.
Bahan SPECTRA yang kuat dan kaku menunjukkan ubah bentuk yang tinggi pada waktu rehat, iaitu, ia meregang dengan kuat sebelum pecah; sifat ini membolehkan sejumlah besar tenaga hentaman diserap. Honeywell mendakwa bahawa komposit serat SPECTRA menunjukkan prestasi yang sangat baik di bawah hentaman halaju tinggi seperti peluru senapang dan gelombang kejutan. Menurut syarikat itu, "Serat canggih kami bertindak balas terhadap kesan dengan mengeluarkan tenaga kinetik dengan cepat dari zon hentaman … ia juga mempunyai peredam getaran yang baik, ketahanan yang baik terhadap ubah bentuk berulang dan ciri geseran dalaman serat yang sangat baik bersama dengan ketahanan yang sangat baik terhadap bahan kimia, air dan cahaya UV."
Dalam teknologi SHIELD, Honeywell menyebarkan helai serat selari dan mengikatnya bersama-sama dengan meresapi mereka dengan resin maju untuk membuat pita searah. Kemudian lapisan pita ini diletakkan melintang pada sudut yang dikehendaki dan pada suhu dan tekanan tertentu, disolder ke struktur komposit. Untuk aplikasi yang boleh dipakai lembut, ia dilaminasi di antara dua lapisan filem telus nipis dan fleksibel. Oleh kerana gentian tetap lurus dan selari, mereka menghilangkan tenaga hentaman dengan lebih berkesan daripada jika ditenun menjadi kain tenunan.
Short Bark Industries juga menggunakan SPECTRA SHIELD dalam pengawal BCS (Ballistic Combat Shirt) untuk sistem SPS TEP. Short Bark mengkhususkan diri dalam perlindungan lembut, pakaian dan aksesori taktikal.
Menurut Honeywell, tentera memilih elemen pelindung yang terbuat dari bahan-bahan ini setelah mereka menunjukkan prestasi yang lebih baik daripada rakan serat aramid mereka.