Perang dikenali sebagai mesin kemajuan terbaik. Industri tangki Kesatuan Soviet membuat lompatan kualitatif yang memusingkan hanya dalam beberapa tahun perang. Mahkota sebenarnya ini adalah kereta kebal siri IS.
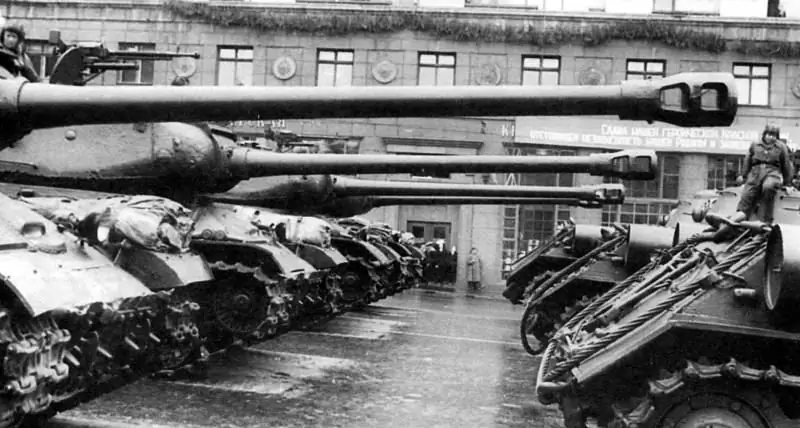
Resipi Magnitogorsk
Dalam bahagian cerita sebelumnya, ia mengenai perisai pelindung kekerasan tinggi 70L yang digunakan untuk menara kereta kebal IS. Pembangun perisai dari TsNII-48 jauh dari pengalaman pertama dalam membuat perlindungan untuk kereta kebal berat.
Sebelum Kursk Bulge, yang menjadi pemangkin pembangunan bangunan tangki berat domestik, objek utama pemodenan adalah tangki KV. Pada mulanya, semua kerja bertujuan untuk mengurangkan bahagian aditif paduan langka dalam komposisi perisai. Malah nama dalam TsNII-48 muncul dengan nama yang sesuai - keluli aloi ekonomi. Perisai asli jenama FD-7954, dengan tangki KV memasuki Perang Patriotik Besar, mengandung, menurut keperluan teknikal, hingga 0,45% molibdenum, 2,7% nikel dan kromium.
Pada akhir tahun 1941, sekumpulan penyelidik yang diketuai oleh Andrei Sergeevich Zavyalov di Institut Perisai membuat resipi untuk baja FD-6633 atau 49C, di mana molibdenum tidak memerlukan lebih daripada 0.3%, kromium - hingga 2.3%, dan nikel - hingga 1, 5%. Memandangkan bahawa tangki siri KV dari separuh kedua 1941 hingga 1943 dikumpulkan kira-kira 4 ribu salinan, seseorang dapat membayangkan jumlah penjimatan sebenar dalam logam paduan.
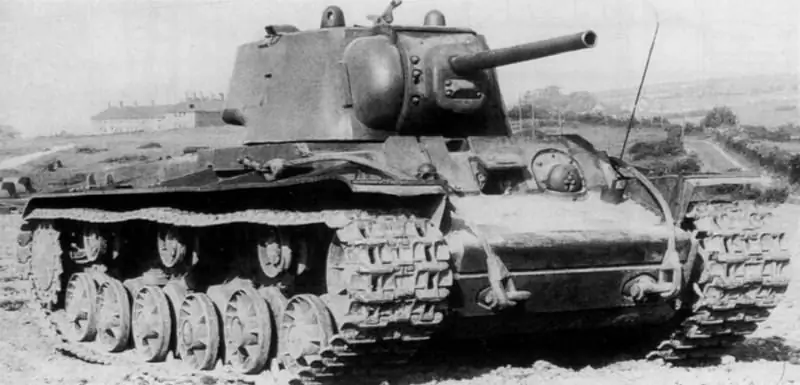
Rahsia kejayaan
Rahsia kejayaan ahli metalurgi terletak pada kajian parameter pembentukan fraktur berserat perisai - parameter utama rintangan peluru. Ternyata anda boleh melakukan tanpa sebilangan besar unsur paduan dengan hanya mengubah kadar penyejukan perisai semasa pelindapkejutan. Tetapi ini mudah dalam kata-kata - berapa banyak eksperimen awal dan peleburan logam yang harus dilakukan, hanya arkib yang diklasifikasikan sekarang yang dapat memberitahu.
Di Magnitogorsk Metallurgical Plant pada tahun 1941, prototaip pertama dari keluli 49C diperoleh, yang tidak kalah dengan perisai tradisional "pra-perang". Khususnya, penembakan oleh meriam 76 mm menunjukkan kepatuhan penuh dengan keperluan taktikal untuk tangki. Dan sejak tahun 1942, hanya baju besi dengan nama 49C digunakan untuk siri KV. Perlu diingat bahawa penggunaan kromium, molibdenum dan nikel telah menurun dengan ketara.
Pencarian formulasi perisai baru untuk alat berat tidak berakhir di sana. Pada tahun 1942 baja GD-63-3 "dikimpal", sama sekali tanpa kromium dan nikel yang jarang. Pada tahap tertentu, nikel digantikan oleh mangan - bahagiannya meningkat lebih dari tiga kali (sehingga 1.43%). Prototaip perisai baru dilancarkan. Dan ternyata ternyata sangat sesuai untuk digunakan secara besar-besaran dalam reka bentuk KV. Tetapi kereta kebal Klim Voroshilov dengan perisai kekerasan sederhana akan berhenti. Dan tempat kenderaan berat diambil oleh kenderaan "Joseph Stalin" dengan perisai kekerasan tinggi.
Perisai bergulung 51C
Sekiranya perisai 70L untuk menara IS-2 dapat dilemparkan, maka helah ini tidak berfungsi dengan bahagian tangki kapal tangki. Di sini, para jurutera menghadapi dua masalah sekaligus - penciptaan perisai kekerasan tinggi dengan ketebalan yang besar dan keperluan untuk mengelasnya ke dalam lambung siap.
Setiap orang yang berminat mungkin sudah mengetahui masalah yang disebabkan oleh pengelasan perisai T-34 - terdapat kebarangkalian keretakan yang tinggi di kawasan kimpalan. IS-2 tidak terkecuali. Dan badannya pada mulanya sepatutnya dimasak dari bahagian yang akhirnya dirawat panas.
Menyedari apa kesukaran dan bahaya yang boleh dibawa oleh penyelesaian teknologi dalam operasi ketenteraan, pakar TsNII-48 mengubah kitaran pengeluaran tangki. Akibatnya, pada tahun 1943, di Ural Heavy Machine Building Plant dan Chelyabinsk Plant No. 200, lambung IS-2 diputuskan untuk dimasak dari pelat perisai yang hanya dilalui percutian tinggi setelah bergolek. Sebenarnya, lambung tangki berat dipasang dari besi "mentah". Ini mengurangkan kecacatan kimpalan pada perisai bergulung dengan kekerasan tinggi 51C.
Rawatan haba terakhir dengan pemanasan sebelum pelindapkejutan sudah dilakukan pada badan tangki yang dikimpal, setelah sebelumnya mengukuhkannya dengan penyangga dalaman. Mayat disimpan di dalam ketuhar selama tiga jam. Dan kemudian, pada peranti khas, mereka dipindahkan ke tangki pelindapkejutan air dan disimpan di dalamnya selama 15 minit. Lebih-lebih lagi, suhu air di tangki pelindapkejutan meningkat dari 30 hingga 55 ° C. Suhu permukaan badan setelah dikeluarkan dari air adalah 100-150 ° С. Bukan itu sahaja.
Setelah pendinginan, badan segera mengalami tempering rendah di tungku beredar pada suhu 280-320 ° С dengan menahan setelah mencapai suhu ini selama 10-12 jam. Pemanasan rendah menara cor dari perisai 70L dilakukan dengan cara yang serupa. Menariknya, kawalan retak di lambung IS-2 eksperimental berlangsung selama empat bulan, ketika tangki pengeluaran pertama meninggalkan pintu kilang.
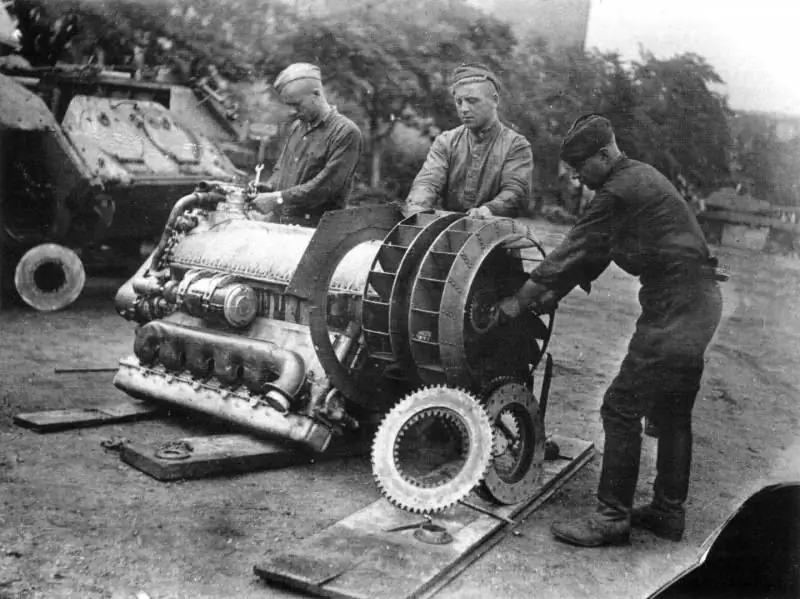
Komposisi kimia
Apakah perisai gulung 51C yang menjadi yang utama untuk IS-2, ISU-122 dan ISU-152? Ini adalah keluli pengerasan yang mendalam untuk ketebalan perisai yang besar dengan komposisi kimia berikut (%):
C 0, 18-0, 24
Mn 0, 70-1, 0
Si 1, 20-1, 60
Cr 1, 0-1, 5
Ni 3.0-3.8
Mo 0, 20-0, 40
P ≤0.035
S ≤0.035.
Sebagai perbandingan dengan pelindung besi 70L, keluli tergulung 51C mempunyai bahagian molibdenum dan nikel yang lebih tinggi, yang menjamin peningkatan kekerasan hingga 200 mm. Ketika lambung tangki berat ditembakkan dengan cangkang 88 mm, ternyata perisai kekerasan tinggi jauh lebih unggul dalam ketahanan daripada pendahulunya kekerasan sederhana. Masalah meletakkan perisai bergulung 51C diselesaikan segera.
Kimpalan pintar
Sumbangan penting untuk kejayaan pembangunan perisai tangki siri IS dibuat dengan pengelasan automatik keluli di bawah lapisan fluks. Oleh kerana mustahil untuk memindahkan keseluruhan proses pembuatan lambung perisai tangki ke pengelasan seperti itu pada awal tahun 1944, para jurutera menumpukan pada mengautomasikan jahitan yang paling banyak diperluas dan mekanikal.
Di kilang Chelyabinsk No. 200, dalam proses pemasangan lambung tangki berat IS-2, hanya 25% dari semua pengelasan yang dapat dilakukan secara automatik. Pada pertengahan 1944, Tankograd dapat mengotomatisasi 18% daripada semua kemungkinan 25% kimpalan. Panjang keseluruhan jahitan yang dikimpal di sepanjang lambung tangki berat IS-2 adalah 410 meter larian, di mana 80 meter larian dilakukan dengan kaedah kimpalan automatik.
Hasil ini telah menghasilkan penjimatan yang besar dalam sumber daya dan elektrik yang kekurangan. Adalah mungkin untuk membebaskan sehingga 50 tukang las manual yang berkelayakan (kos tenaga kerja mereka dalam jumlah 15,400 jam kerja) dan menjimatkan 48,000 kilowatt-jam elektrik. Pengurangan penggunaan elektrod (kira-kira 20,000 kg, austenit - 6,000 kg), oksigen (sebanyak 1,440 meter padu).
Masa yang dihabiskan untuk mengimpal juga dikurangkan dengan ketara. Sebagai contoh, mengimpal bahagian bawah dan kotak turet ke sisi dengan jahitan enam belas meter mengambil masa 9.5 jam manusia dalam mod manual, dan hanya 2. Jahitan yang sama panjangnya menghubungkan bahagian bawah ke sisi lambung tangki dalam mod automatik diperlukan 3 jam kerja (dalam manual 11, 4). Pada masa yang sama, tukang las berkemahiran tinggi dapat digantikan oleh pekerja yang tidak mahir dalam pengelasan automatik.
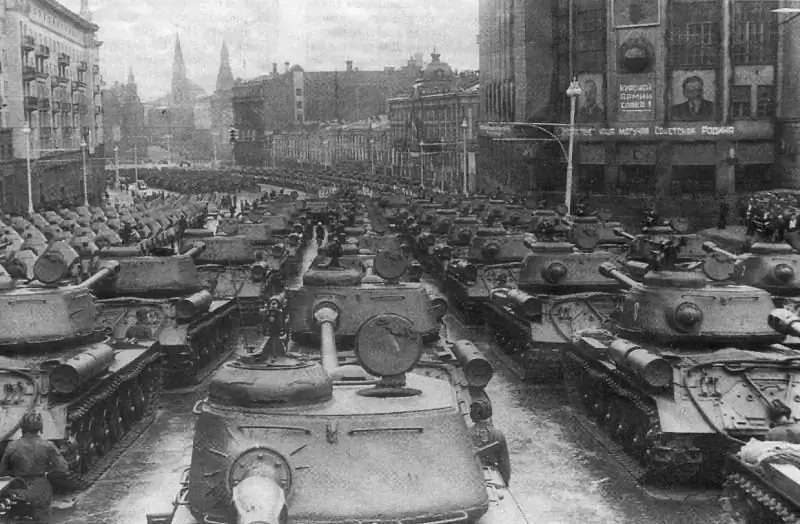
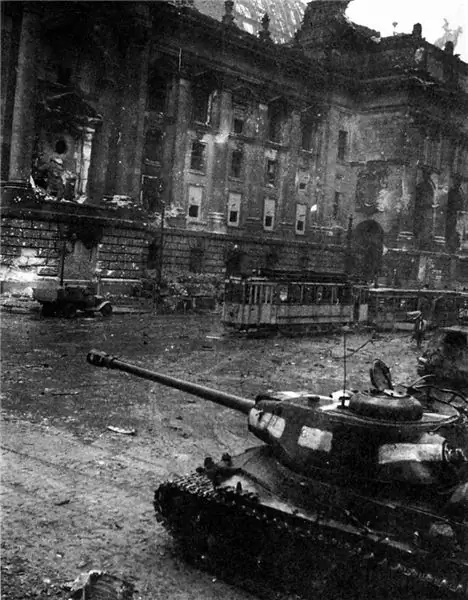
SAG Ural
Penyelidik industri tangki Soviet, calon sains sejarah Zapariy Vasily Vladimirovich dari Institut Sejarah dan Arkeologi Cawangan Ural Akademi Sains Rusia dalam salah satu karyanya menerangkan dengan terperinci unit kimpalan automatik yang digunakan di Ural untuk berperisai pengeluaran lambung.
Yang paling meluas adalah senapang serangan jenis "ACC" dengan kepala Bushtedt. Terdapat lapan pemasangan seperti itu di Uralmash. Kelajuan umpan wayar di mesin ini bergantung pada voltan di arka. Ia memerlukan 5 unit, termasuk 3 motor elektrik kinematik dan 1 penjana motor.
Menjelang pertengahan tahun 1943, mesin kimpalan SA-1000 telah dirancang untuk keperluan tangki berat IS-2. Atau mesin kimpalan dengan kapasiti sehingga 1000 A.
Untuk menguasai pengeluaran lambung berperisai untuk tangki berat Chelyabinsk IS-3 yang baru, para jurutera kilang pada tahun 1944 merancang alat tersebut "SG-2000". Mesin ini dirancang untuk berfungsi dengan kabel kimpalan karbon rendah dengan diameter yang meningkat (6-8 mm) dan mendapati aplikasinya dalam pembuatan menara IS-3. Pemasangan mempunyai dispenser untuk memperkenalkan komposisi khas (pelbagai ferroalloy) ke bahagian kimpalan untuk menyahtoksin (memulihkan) logam di dalamnya. Secara keseluruhan, berdasarkan prinsip pengaturan diri arka kimpalan di UZTM, pada tahun 1945, 9 pemasangan kimpalan automatik dari tiga jenis telah dibuat: "SA-1000", "SG-2000", "SAG" ("Kimpalan automatik kepala ").
Lebih cantik daripada baju besi Jerman
Hasil keseluruhan cerita dengan perisai kereta kebal IS berat adalah pengembangan cepat dari resipi baja yang melebihi perisai Jerman dalam sifat taktikalnya. TsNII-48 menerima keluli 120 mm yang dapat dikeraskan, ketebalannya, jika perlu, dapat ditingkatkan hingga 200 mm.
Ini menjadi asas utama untuk pengembangan keluarga pasca perang tank Soviet yang berat.